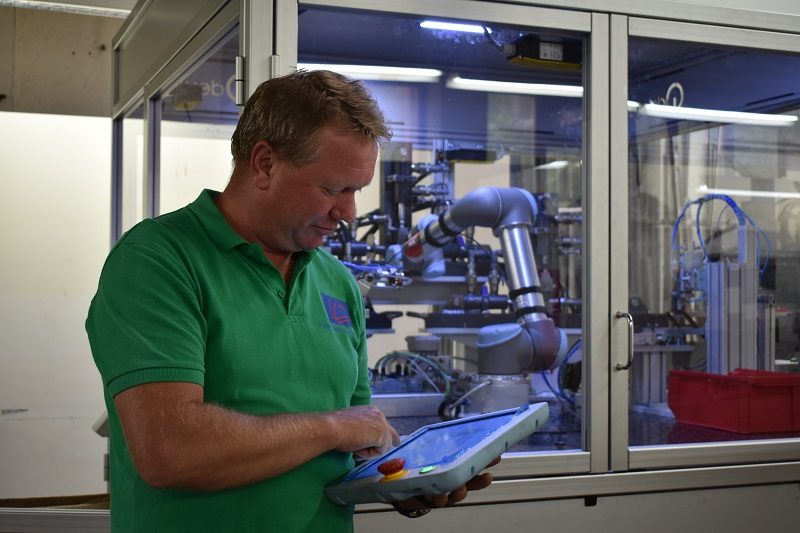
To increase the level of digitalization, relieve employees, and set new standards for knowledge transfer, Viper Tube Systems launched a digitalization process in December 2020. The project is supported by the DigiInvest funding of the state with €30,000 (total project volume over €100,000), lifting internal processes to level 4.0. “Digitalization is an essential aspect of today’s business environment. Therefore, we would have implemented our production 4.0 plans anyway, even without the funding approval. However, the funding certainly makes it easier to explore this unknown path,” says Managing Director Petra Hallinger.
Viper Tube Systems from Bischofshofen is not new to the field of digitalization. For example, the company introduced an ERP system with automatic accounting 15 years ago. Today, they are far more advanced and rely on production processes 4.0. The related digitalization project is based on three pillars: learning cameras for quality assurance, full automation, and an e-learning app. Viper Tube Systems processes around 200,000 ring soldered pieces annually, which have two sealing surfaces. Currently, visual inspection is carried out with the four-eye principle. Soon, quality control will be performed using learning cameras. This will improve the quality of the optical measurement and testing process and relieve employees as the task is very exhausting for them.
In addition, unnecessary waste is to be avoided in the future by fully automating the impulse bending production. Cameras are also installed for continuous monitoring and a bunker that stores material. This eliminates manual reloading by one person, and the machine can run around the clock. Currently, the machines are still running in shifts. The communication function expands production: if irregularities occur, the responsible employees are automatically informed and can counteract the problem. A new e-learning app revolutionizes knowledge management in the company: training, quality assurance records, documentation, and processes are now carried out digitally. This goes so far that employees can also take a digital test on the learned training content.
Quick response to new challenges
When asked about the impact of the pandemic on her company, Petra Hallinger reports that “in spring 2020, the supply chain was disrupted and we, like our customers, were forced to implement short-time work.” However, production could resume as early as June. “We then worked with our company physician to develop and implement safety rules. Even today, one year later, the supply chain is still very fragile. Every day brings new challenges that we have to respond to quickly,” Hallinger continues. The company’s daily operations have adapted to the new circumstances: Viper Tube Systems increasingly uses online meetings, and trade show visits or trainings are also held virtually. In addition, working from home has become established for certain employees.
About Viper Tube Systems
The company based in Bischofshofen (Pongau) has around 60 employees and produces metal tubes for the automotive and commercial vehicle industries. In December 2020, they started a digitalization process with the support of the DigiInvest funding program, which will run until May 2022.
This might also interest you
6. March 2025
salz21: Necessary Steps for the Future
On March 5, 2025, salz21 | Home of Innovation once again provided a platform for future topics, innovations, and interdisciplinary exchange. More than 1,000 visitors took the opportunity to learn about current developments and discuss perspectives for tomorrow. Three topics were particularly dominant: climate protection, artificial intelligence, and a strong Europe.
25. September 2024
Green Deal: How Sustainable Business Development Can Look
The EU aims to create political and legal frameworks through the Green Deal to transform both the economy and society in a sustainable way. The Pinzgau-based company Design Composite demonstrates how this can be implemented.
15. August 2024
Sunbeam Yachts: Where Craftsmanship Meets Digitalization
Sunbeam Yachts has been building exclusive sailing yachts at Mattsee for generations. The production is done by hand, with some processes now digitally supported.
12. August 2024
SBS: One Software for Many Self-Service Devices
As a leading provider of banking software in Salzburg, SBS is now exploring new markets. The company remains true to its core segment by offering manufacturer-neutral software for self-service devices in additional sectors.