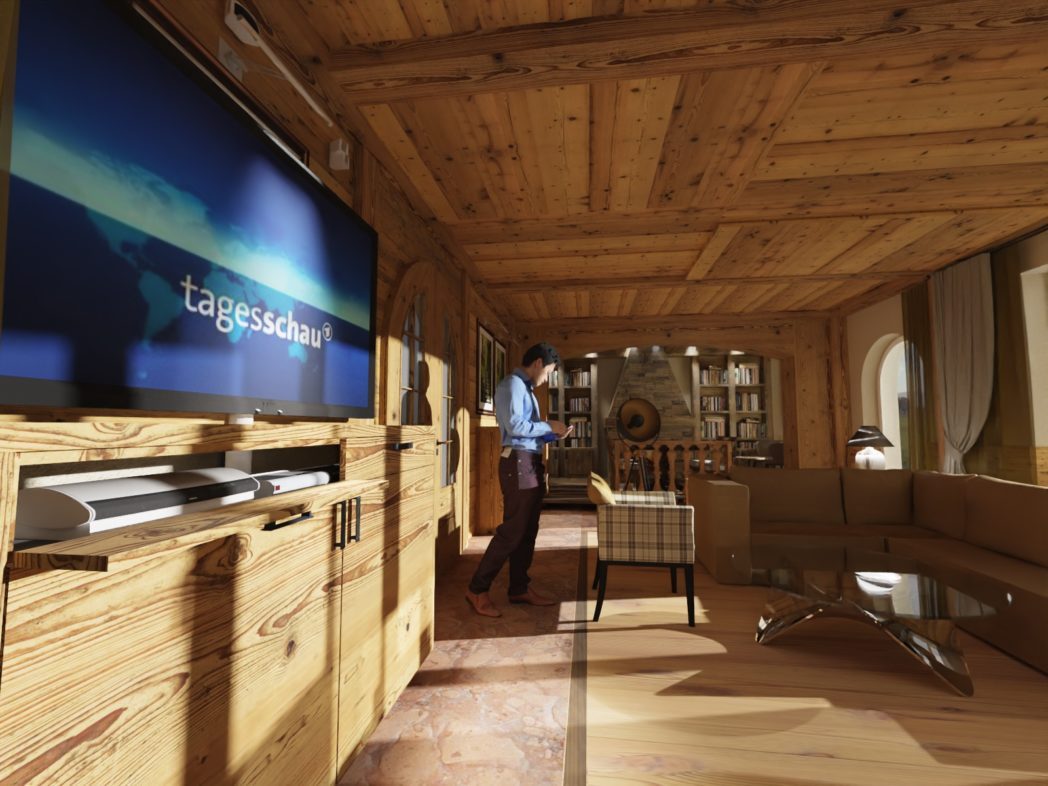
The joinery Philipp Haas + Söhne has a long history. The company was founded in 1958 in Bad Reichenhall in the Berchtesgadener Land region. In 1996, a joinery in Unken in the Salzburg region was added. The two joineries are separate businesses but work closely together for project orders, and also involve partner companies. This approach has put them on the path to success. They have completed many exceptional projects in recent years, such as furnishing Schloss Elmau and creating the conference table for the G7 summit held there. Entire luxury hotels have also been equipped with the joinery’s wooden products.
But the joinery craft is difficult, and it is a challenge to assert oneself in the highly competitive furniture market. A few years ago, the managing directors and brothers Johannes and Friedrich Haas faced the decision: to grow or to yield? They chose the former. The goal was to grow beyond the status of a small traditional joinery.
Extended digital workbench
Since that decision, a wave of digitalization has transformed the two businesses from the ground up. One of the first and most important steps was to integrate partner companies into a digital system. Philipp Haas + Söhne work with a large partner network. This enables them not only to sell individual joinery products but also to offer a wide range of services. They can produce and cover the planning and design of furniture and furnishings for entire houses and hotels. At Haas, experts from interior design, architecture, and project development work together. The Haas master workshops with their partner companies then take over the production of entire furnishings.
“The extended workbench, i.e., suppliers who deliver pre-fabricated parts to us, is essential for our growth and success,” says Friedrich Haas. Order data is sent to suppliers, lighting designers, architects, and partner companies in glass and metal processing. This allows for seamless communication between the businesses. In the past, orders, quotes, and invoices were handwritten and then typed. Drawings for production and material lists for suppliers were also done by hand. With digital support, all of this is now automated. The plans are also available digitally. Data such as measurements and materials are directly fed into the CNC machine, which can automatically manufacture the workpieces with high precision. By networking the entire supply chain, the joineries can produce faster, more productively, and cost-effectively.
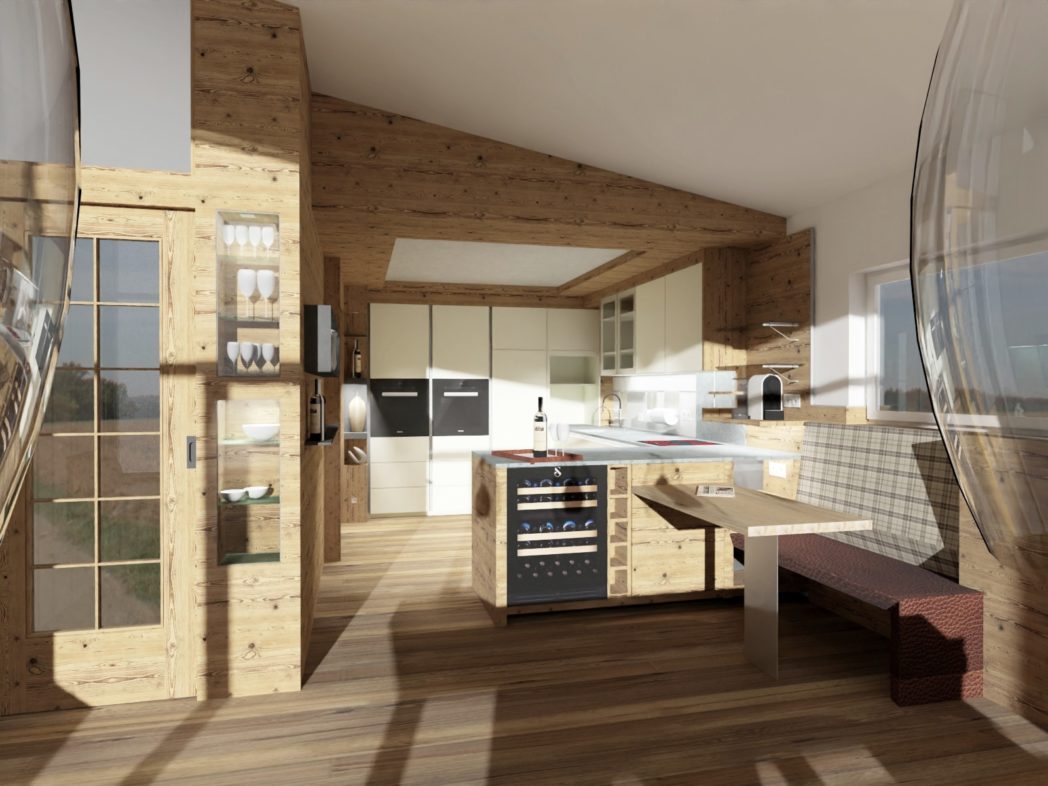
The networking gene of the Haas brothers
The network of partner companies is the great strength of Philipp Haas + Söhne. “As brothers who grew up in a large family with eight children, networking is in our genes, so to speak.” The company can accept orders that other carpentry businesses cannot handle. Large orders, such as furnishing an entire hotel, can be completed in a short time. “Through digitization, we can bundle and bring together all information and manufacture and deliver the product to customers on time,” says Friedrich Haas. In some years, Philipp Haas + Söhne are now the sole provider for approximately eighty percent of their orders, as not many carpentry businesses can offer the service, such as the interaction between production and architecture and interior design. Through the network, the carpentry business obtains the capacity for large orders. Their decentralized structures make them very flexible in this regard.
Customer service in 3D
However, Friedrich and Johannes Haas were not satisfied with digitizing the supply chain alone. Philipp Haas + Söhne also relies on digital support in the area of customer service. For example, if furniture is designed for a customer’s home, they can view the furniture through 3D visualization. Customers are thrilled with this and gain more planning security.
Salzburg promotes investments
Overall, Friedrich and Johannes Haas have already invested 1.5 million euros in digitization projects, expanding office and warehouse space, and building a sample apartment in the Austrian facility. They have also benefited from the digital promotion of the state of Salzburg. “We are very impressed by the support that an internationally active company in Austria receives,” says Friedrich Haas.
However, craftsmanship always remains at the forefront. This is the core competency on which the carpentry business relies. In the end, what counts for customers is always the finished product.
That might also interest you
6. March 2025
salz21: Necessary Steps for the Future
On March 5, 2025, salz21 | Home of Innovation once again provided a platform for future topics, innovations, and interdisciplinary exchange. More than 1,000 visitors took the opportunity to learn about current developments and discuss perspectives for tomorrow. Three topics were particularly dominant: climate protection, artificial intelligence, and a strong Europe.
25. September 2024
Green Deal: How Sustainable Business Development Can Look
The EU aims to create political and legal frameworks through the Green Deal to transform both the economy and society in a sustainable way. The Pinzgau-based company Design Composite demonstrates how this can be implemented.
15. August 2024
Sunbeam Yachts: Where Craftsmanship Meets Digitalization
Sunbeam Yachts has been building exclusive sailing yachts at Mattsee for generations. The production is done by hand, with some processes now digitally supported.
12. August 2024
SBS: One Software for Many Self-Service Devices
As a leading provider of banking software in Salzburg, SBS is now exploring new markets. The company remains true to its core segment by offering manufacturer-neutral software for self-service devices in additional sectors.